Lighting with the help of 3D printing
Source: eKapija
Wednesday, 14.12.2022.
12:50


(Photo: Signify)

Signify has applied this technology for manufacturing custom-made luminaires.
What does this mean?
You can choose on your own, or with the help of Signify experts, all the details according to your needs, from the luminaire type, through colour and texture, and Signify will turn that idea to 3D printed luminaires made of 100% recycled polycarbonate.
(Photo: Signify)

How does the process work?
Step 1: You define the shape, size and material. You can do it online using the website, or live in alignment with experts. Various shapes and materials are available allowing you to have a unique product which will diferentiate you from others.
Step 2: Then you choose the texture and pattern. Whether you prefer lines, woven, technology grooves, or just normal finish - it’s all possible.
Step 3: The next step is to choose the right lumen output, driver settings, optics and other options for your future lighting.
Step 4: And finally, you only need to confirm the design and the printing can start!
VIDEO:
By choosing LED lighting, you have already made your contribution to sustainability goals. 3D printed lighting from Signify will help you make even more impact. Our products are designed for a circular economy and have a lower carbon footprint.
Our 3D printed luminaires are printed with a 100% recyclable polycarbonate and are designed to be fully re-used at the end of their lifetime, avoiding waste of material.
Compared to traditional luminaires, our smart innovative circular designs use no paint, less parts and less screws.
We only print it when you need it to avoid large stock storage. Due to the light weight of polycarbonate, less energy is used during transportation which drastically reduces CO2 emissions.
Compared to traditional aluminium die casting production methods, 3D printing requires far less energy and material. This brings you a reduction up to 75% on your carbon footprint.
(Photo: Signify)

Together with the reduced transportation footprint and the standard use of LED lights, 3D printed luminaires are the most energy efficient choice. Hence, energy saving in production and transport is achieved as well as during the work of the luminaire, but also the reduction of waste with circular approach and use of recycled materials for manufacturing the housing of the luminaire.
(Photo: Signify)

Due to the above said, 3D printed lighting can significantly help in achieving sustainability goals for those companies which strive to become, or are already „green“.
Companies:
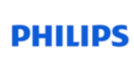
Tags:
Signify
3D printed lighting
energy conservation
energy efficiency
circular economy
sustainable development
3D printed luminaires
special edition newsletter
Interior and Exterior Solutions for a Modern Practical and Comfortable Space
Comments
Your comment
Most Important News
Full information is available only to commercial users-subscribers and it is necessary to log in.
Follow the news, tenders, grants, legal regulations and reports on our portal.
Registracija na eKapiji vam omogućava pristup potpunim informacijama i dnevnom biltenu
Naš dnevni ekonomski bilten će stizati na vašu mejl adresu krajem svakog radnog dana. Bilteni su personalizovani prema interesovanjima svakog korisnika zasebno,
uz konsultacije sa našim ekspertima.